Welcome to our comprehensive guide on understanding labor costs for fence installation. Whether you’re looking to boost your property’s privacy, security, or curb appeal, adding a fence is a great investment—but figuring out how much the labor will cost can be confusing. From the type of materials you choose to the size of your yard and even the terrain, several factors can affect the price you’ll pay for professional installation. In this post, we’ll break down everything you need to know about how labor costs are calculated, what influences those rates, and how to get the best value for your budget. By the end, you’ll have a clear understanding of what to expect when hiring a professional or even tackling the project yourself.
On average, labor for fence installation costs between $10 to $30 per linear foot, depending on factors such as the type of fence, terrain, and location. More complex materials like vinyl or wrought iron typically incur higher labor costs, while simpler installations like chain link fences are often on the lower end of the scale.
Table of Contents
Factors That Affect Labor Costs For Fence Installation
When planning for fence installation, it’s crucial to understand that labor costs can fluctuate based on several factors. Each element of the installation process—such as the type of material, the project’s size, terrain conditions, and even the location—can impact the overall labor cost. Below, we’ll break down these key factors in detail to help you better estimate your fencing project’s budget.
Factors That Affect Labor Costs for Fence Installation
Fence Material
One of the primary factors influencing labor costs is the type of material you choose for your fence. Different materials not only have varying price points for purchase but also require different installation techniques, which can significantly impact labor time and complexity.
- Wood: Wood fences often require precise measurements and cutting, and additional tasks such as staining or painting can extend labor time. Installation is generally more hands-on, making labor costs higher compared to simpler materials.
- Vinyl: Vinyl fencing comes in prefabricated panels, which simplifies installation. While the material cost is generally higher, the reduced labor time can make up for it, leading to a more balanced overall cost.
- Chain Link: This is one of the easiest and quickest types of fences to install. Because it’s relatively straightforward, labor costs for chain link fences tend to be on the lower end.
- Aluminum: Aluminum fences require more careful handling and precise installation due to their durability and design. Although installation may take longer, it offers longevity and lower maintenance needs, which can be a long-term benefit despite higher upfront labor costs.
Each material requires specialized skills and tools, impacting both the time and effort required, which directly influences labor costs.
Fence Length and Height
The size of the fence project—particularly its length and height—also plays a crucial role in labor costs. It’s simple: the larger the fence, the more time and effort it will take to install, leading to higher labor costs.
- Example: “A taller or longer fence takes more time and effort to install, which means higher labor costs.”
A longer fence requires more posts, panels, and materials, while a taller fence often involves more structural support. Both scenarios will increase the labor required for completion. Additionally, taller fences can demand more complex installation techniques, such as the need for stronger foundations or special permits, which can add to the cost.
Terrain and Site Preparation
The condition of the land where the fence will be installed can have a significant impact on labor costs. Flat, even terrain is the easiest to work on, while difficult landscapes may require additional preparation that increases both time and cost.
- Slopes and uneven ground: Installing a fence on a sloped or uneven surface requires extra work to ensure proper alignment and support. Workers may need to level the ground or use specialized tools and techniques to handle the slope, which adds to labor time.
- Rocky or hard soil: Digging post holes in rocky or compact soil can be challenging and time-consuming, increasing labor costs. In some cases, heavy-duty equipment might be required, further driving up the overall cost.
- Vegetation and obstacles: If the site is covered in heavy vegetation or has existing obstacles like old fencing or large trees, clearing the area adds another layer of labor. Removing old fences or leveling the land can add several hours—or even days—to the project, further driving up labor costs.
In short, the more challenging the terrain, the more costly the labor becomes, as workers must spend additional time preparing the site before installation can even begin.
Location and Regional Differences
Labor costs for fence installation can vary significantly depending on your geographical location. Regional factors, including the cost of living and demand for labor, influence how much you’ll pay for installation.
- Urban areas: Cities like Los Angeles, New York, or San Francisco typically have higher labor rates due to the higher cost of living. Contractors in these areas often charge more for their services, which directly impacts labor costs for your fencing project.
- Rural areas: In contrast, rural areas usually offer lower labor rates. However, depending on the location, additional travel fees may apply if the contractors need to bring materials or equipment from a distant supplier.
- Example: “In cities like Los Angeles or New York, higher labor rates due to the cost of living can make installation pricier than in rural areas.“
Furthermore, some regions have different building codes, permit requirements, or environmental regulations, all of which can affect labor time and costs. In areas with stringent regulations, contractors may need to spend extra time ensuring that the installation complies with local laws, increasing the overall labor expense.
Understanding the factors that affect labor costs for fence installation can help you make more informed decisions about your project. From the material you choose and the size of the fence to the complexity of the terrain and your location, each aspect plays a role in determining the final cost. By considering these elements, you can better estimate your budget and ensure that your fencing project proceeds smoothly.
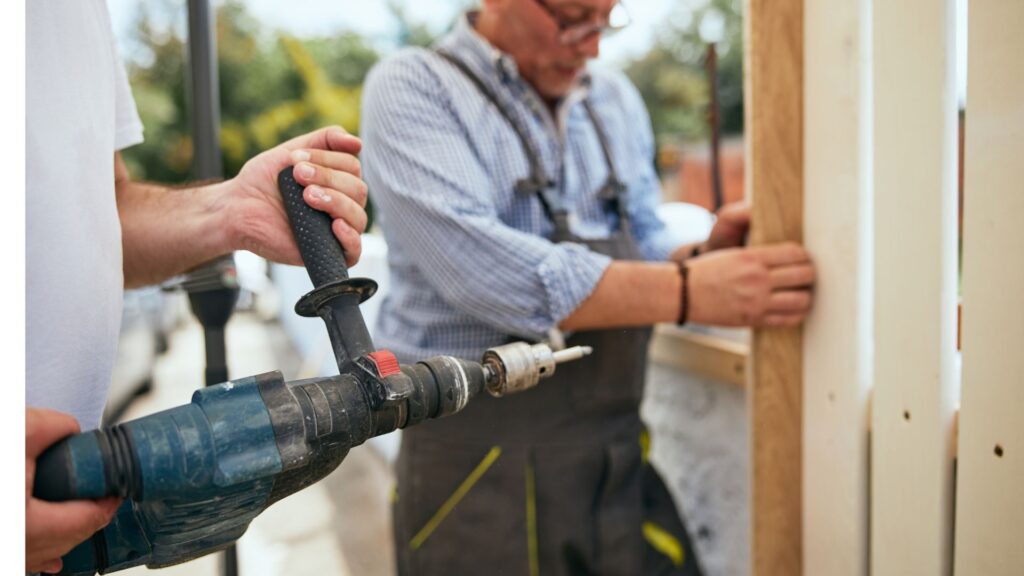
Average Labor Costs For Different Types Of Fences
When planning a fence installation, understanding the breakdown of labor costs is crucial for budgeting. Labor fees can significantly vary depending on the fence material, complexity of the installation, and location. Below is a detailed look at labor costs for different fence types, helping you make informed decisions before hiring a professional.
Wood Fence Installation
Wood fences are a classic and popular choice, offering a natural aesthetic that complements many homes. The labor cost for wood fence installation typically ranges between $10 to $30 per linear foot. However, the actual cost will depend on various factors, including the complexity of the design, the type of wood used (e.g., cedar, pine, redwood), and whether the fence is built with simple vertical slats or more intricate patterns like latticework.
For instance, basic wood fences that consist of standard vertical boards will generally fall on the lower end of the price range, around $15 to $20 per linear foot. On the other hand, custom or decorative wood fences, such as those featuring complex patterns or post caps, will likely require more time and craftsmanship, pushing labor costs towards $25 to $30 per linear foot.
- Example: “For a wood fence, you might expect to pay $15-$25 per linear foot in labor, depending on the complexity of the design and material.“
Vinyl Fence Installation
Vinyl fencing has become a popular option for homeowners looking for a low-maintenance and durable solution. However, vinyl fences come with labor costs that range from $15 to $40 per linear foot. This price is higher than wood fencing, in part because vinyl requires more precise installation.
Vinyl fence panels are typically pre-manufactured, and aligning them perfectly is critical for both the look and stability of the fence. Any small error in the placement of posts or panels can affect the durability, requiring careful measurement and skilled labor. This attention to detail during installation is one of the reasons why vinyl fences come with a higher labor cost, especially for larger properties.
Additionally, vinyl fencing can be more time-consuming to install in uneven terrain or if the property requires custom cut panels to fit certain angles or slopes. While vinyl fences do cost more upfront in terms of both material and labor, the long-term savings on maintenance (as they won’t rot or require painting) often offset the initial investment.
Chain Link Fence Installation
Chain link fences are one of the most cost-effective fencing options for both material and labor. The labor cost typically falls between $7 to $20 per linear foot, making it a go-to choice for budget-conscious homeowners or for fencing large areas, such as backyards, commercial properties, or sports fields.
The installation process for chain link fencing is generally faster than other types of fences. This is largely due to the fence’s simple design, which usually involves digging post holes, installing the posts, and then attaching the chain link material. The straightforward nature of this installation reduces labor time, which is why chain link fencing is among the most affordable options.
However, factors such as the terrain of the property and the need for additional features, like gates or privacy slats, can increase labor costs slightly. Nonetheless, for a quick and affordable fencing solution, chain link remains an excellent option for many homeowners.
Aluminum or Metal Fence Installation
Aluminum and wrought iron fences are considered premium fencing options due to their high-end appearance and durability. As such, the labor costs for installing metal fences tend to be significantly higher than other materials, ranging from $20 to $50 per linear foot. This increase in labor cost is primarily due to the specialized skills and time required to install metal fences properly.
Aluminum fences are often lighter but still require precise placement and alignment to ensure they are securely installed. Wrought iron, on the other hand, is much heavier and may require custom fabrication on-site, especially for ornamental designs or when dealing with uneven landscapes. The weight and intricacy of metal fences add to the labor hours and the need for experienced professionals.
Moreover, metal fences often come with additional complexities, such as mounting brackets or welding for custom designs. These fences might also require permits in certain locations due to their height or design, further contributing to the labor cost.
When considering a new fence installation, it’s important to factor in not only the material costs but also the labor involved. Each type of fence has its own set of challenges and requirements that can impact the overall price, so make sure to get quotes from reputable contractors and ask about the specifics of your project to avoid any surprises.
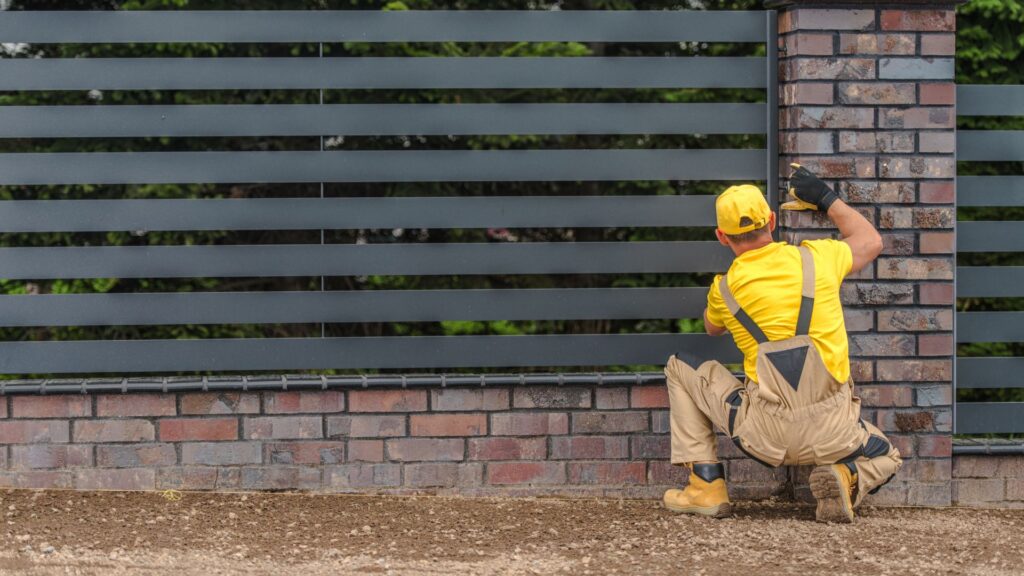
Breakdown Of Labor Costs: What’s Included?
Understanding the breakdown of labor costs when installing a fence is crucial for making informed decisions and planning your budget effectively. Below is a detailed explanation of the key elements that contribute to the overall labor costs when hiring a contractor for fence installation.
Initial Consultation and Site Inspection
Before any actual work begins, most contractors will schedule an initial consultation and site inspection. This visit allows them to assess the area, understand the scope of the project, and identify any challenges like uneven terrain, existing landscaping, or underground utilities. While this consultation may seem like a small step, it is often factored into the total labor cost. Contractors use this time to plan the logistics, determine material requirements, and provide a more accurate cost estimate. Sometimes, the consultation is offered as a complimentary service, but more often, the time and expertise invested here will be rolled into the final labor cost.
Fence Post Installation
Fence post installation is typically one of the most labor-intensive and critical parts of the job. Setting posts involves digging holes, positioning posts at the correct depth and height, and securing them with concrete or gravel. This process requires precision because improperly set posts can compromise the entire fence structure. The type of soil can also impact labor costs—rocky or clay-heavy soil will take longer to work with, increasing both time and effort. Labor costs rise when posts need to be placed in difficult areas or when the fence requires more durable materials. Given the complexity of this step, it’s no surprise that post installation is a significant factor in the overall labor pricing.
Installation of Panels or Pickets
Once the posts are securely in place, the next phase involves attaching the fence panels or pickets. The labor cost for this stage can vary depending on whether pre-fabricated panels are being used or if the fence is built piece by piece with individual pickets. Pre-made panels are quicker to install, which may reduce labor time, but they might not offer the same level of customization. On the other hand, installing individual pickets allows for more customization, but it’s more time-consuming. The more intricate the design, the more time it takes, driving up labor costs. Additionally, factors like the height of the fence and the materials used—wood, vinyl, metal, etc.—will also impact how labor-intensive this part of the process is.
Gates and Other Features
Adding gates, decorative elements, or custom features to your fence can significantly affect labor costs. Installing a gate requires careful alignment to ensure smooth operation, as well as additional hardware and materials, all of which increase both time and complexity. Decorative elements, such as latticework, post caps, or ornamental designs, require skilled labor and extra precision, further driving up costs. Custom designs or features can involve additional planning and special materials, making them more expensive in terms of both time and effort. Contractors typically charge more for these specialized tasks due to the additional expertise required.
Clean-Up and Finishing
Many people overlook the fact that post-installation clean-up and finishing work are also part of the labor costs. After the fence is installed, the worksite needs to be cleared of debris, dirt, and leftover materials. Some contractors include this in their labor cost estimates, while others may charge it as an additional service. Clean-up can involve removing old fencing, grading the site, and even disposing of waste, which requires time and effort. Finishing touches, like painting, staining, or applying weatherproofing treatments, can also add to labor costs, depending on the scope of work required to complete the project.
In conclusion, when evaluating labor costs for fence installation, it’s essential to consider the full range of tasks involved, from the initial consultation to the final clean-up. Each stage requires a different level of skill and time investment, all of which are reflected in the overall pricing. Understanding these factors will help you better assess quotes from contractors and plan your budget accordingly.
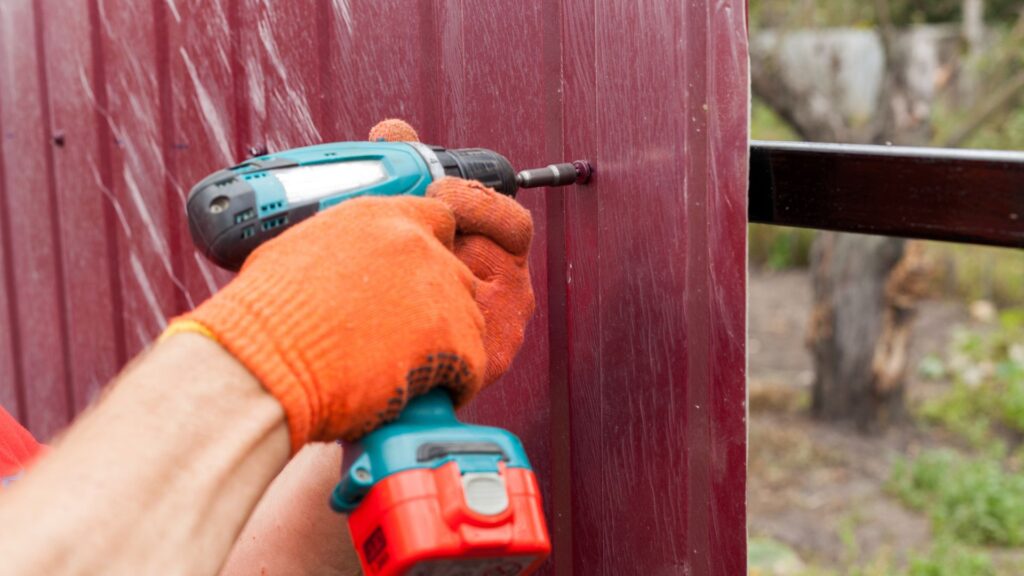
DIY Vs. Hiring A Professional: Pros And Cons
When planning a fence installation, one of the primary decisions you’ll face is whether to take on the project yourself or hire a professional. Both options have their benefits and drawbacks, depending on your budget, experience, and the scope of the project. In this section, we’ll explore the pros and cons of DIY fence installation versus hiring a professional contractor.
DIY Fence Installation
Many homeowners opt for DIY fence installation to save money, and it can indeed be a cost-effective choice. By handling the project yourself, you can eliminate labor costs, which are often a significant portion of the overall expense. However, there are several factors to consider before deciding if the DIY route is right for you.
Potential Cost Savings
DIY fence installation can lead to substantial savings, particularly if you already own the necessary tools and have some construction experience. The price of materials like wood, metal, or vinyl is the main expense, but without the added labor costs, your total investment can be considerably lower.
However, these savings can evaporate quickly if mistakes are made. Incorrect measurements, poorly set posts, or misaligned panels can lead to costly fixes, sometimes requiring more materials or even professional help to rectify. What might seem like a cheap project at first could end up being more expensive than hiring a contractor if not done properly.
Tools and Time Investment
A successful DIY fence installation requires not only the right materials but also the proper tools. Depending on the type of fence, you may need posthole diggers, levels, saws, hammers, and power tools. If you don’t already own these, renting or purchasing them can add to the overall cost.
In addition, consider the time commitment. Installing a fence is labor-intensive, often taking several days or even weeks, depending on the size of your yard and the complexity of the design. If you’re juggling a full-time job or other responsibilities, this time investment could be a significant drawback.
While many DIYers enjoy the satisfaction of completing a home improvement project themselves, it’s essential to weigh whether the potential savings outweigh the time, effort, and risk involved.
- Example: “If you’re handy and have the right tools, a DIY project might save you money—but it can also become more expensive if mistakes are made.“
Professional Fence Installation
On the other hand, hiring a professional to install your fence comes with its own set of advantages. While the upfront cost is higher, due to labor fees, you’re also investing in expertise and convenience.
Benefits of Hiring a Professional
One of the key benefits of hiring a professional is their experience. Fence contractors have the knowledge and skills to handle various challenges that might arise during installation, such as uneven terrain or complex property lines. They also have access to high-quality materials and the right tools, ensuring a sturdy and aesthetically pleasing fence.
Another significant advantage is the speed of installation. Professionals can typically complete a project much faster than a DIYer, as they have a team and the necessary equipment to work efficiently. What might take a weekend warrior several weekends to finish could be completed in a matter of days by a professional crew.
Peace of Mind and Quality Craftsmanship
When you hire a professional, you’re also paying for peace of mind. Many fencing companies offer guarantees on their work, meaning if something goes wrong, they’ll come back and fix it at no additional cost. This level of assurance can be particularly comforting if you’re investing in a high-end fence or live in an area with strict building codes. The quality of craftsmanship you get from a professional is often superior to what most DIYers can achieve, ensuring your fence is both durable and visually appealing.
While labor costs are undoubtedly higher when hiring a professional, you’re paying for a stress-free experience, reliable craftsmanship, and the assurance that the job will be done right the first time.
Hidden Costs of DIY Projects
While DIY projects can save money upfront, there are often hidden costs that homeowners may not initially consider. For example, you may need to rent specialized tools like augers, cement mixers, or power saws if you don’t already own them. Tool rental fees can add up quickly, particularly if your project takes longer than expected.
Additionally, mistakes in measurement or installation can lead to the need for extra materials. Whether it’s buying more fence posts due to incorrect spacing or replacing panels damaged during the process, these unexpected expenses can quickly inflate your budget. Other hidden costs might include purchasing or renting a truck to transport materials, handling disposal of old fencing, or even landscaping repairs if the installation causes damage to your yard.
Finally, there’s also the potential for safety risks. Improperly installed fences can collapse or cause injury, leading to potential medical costs or the need for professional repairs. These are all factors that many DIYers may not consider at the outset, but they can significantly impact the final cost of the project.
In conclusion, the decision between DIY and hiring a professional comes down to weighing the potential cost savings of doing it yourself against the expertise, speed, and peace of mind offered by a professional contractor. While DIY can save you money initially, it’s important to consider the time investment, the need for specialized tools, and the risk of errors that could end up costing you more in the long run. Conversely, hiring a professional offers a faster, more reliable solution, though at a higher upfront cost. The choice ultimately depends on your budget, experience, and how much time you’re willing to dedicate to the project.
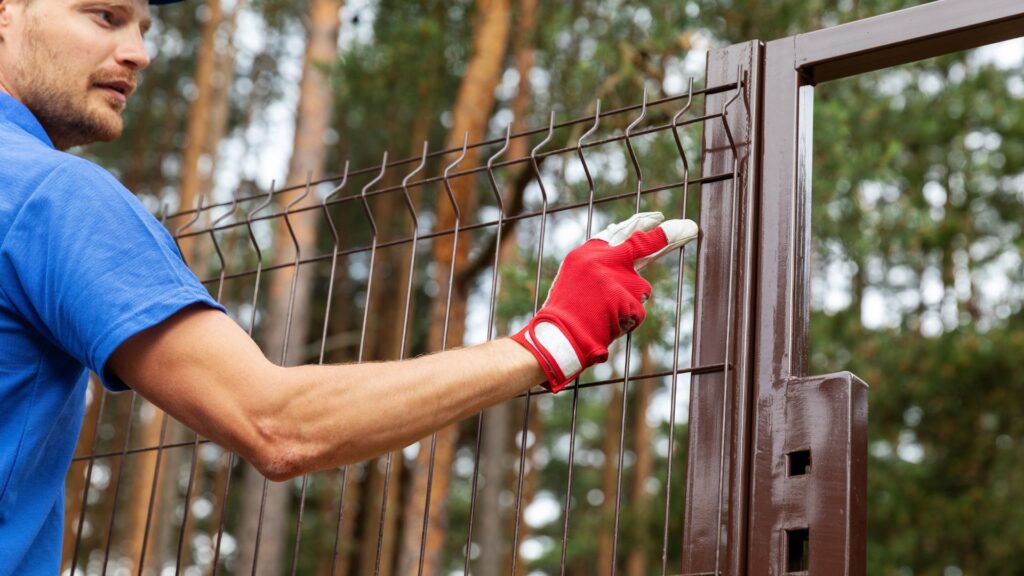
How To Get Accurate Labor Quotes
Getting accurate labor quotes is crucial to ensure you’re not overpaying for a job and that the work meets your expectations. Whether you’re tackling a home renovation, repair, or a larger construction project, taking the right steps when gathering quotes can save you time, money, and stress. Here’s how you can get the most accurate and competitive labor quotes:
Ask for Multiple Quotes
One of the most effective ways to ensure you’re getting a fair price is to obtain multiple quotes from local contractors. It’s generally recommended to collect at least three quotes. This not only allows you to compare prices, but also helps you gauge the professionalism and expertise of each contractor. By doing so, you can avoid getting locked into a higher price than necessary or working with a contractor who may not be the best fit for your project. It’s also a way to see if a contractor is quoting suspiciously low, which could indicate hidden costs or subpar work.
Verify Contractor Credentials
Before you even consider hiring a contractor, it’s important to verify their credentials. This includes checking their license, insurance, and reviews. A licensed contractor is typically more reliable and meets local industry standards. Insurance protects you from being held liable for any injuries or damages that occur during the job. In addition, reading reviews from previous clients will give you insights into the contractor’s reliability, work quality, and professionalism. Hiring a licensed and insured contractor with strong reviews reduces your risk of running into problems down the line, ensuring a smoother project process.
Inquire About Guarantees and Warranties
A good contractor should stand behind their work. When comparing quotes, be sure to ask about any guarantees or warranties they offer. Some contractors provide workmanship guarantees, ensuring that any issues arising from their labor will be addressed within a certain period of time. Others might offer warranties on the materials used. These assurances provide peace of mind that if something goes wrong, you won’t be left footing the bill for repairs or adjustments. When a contractor is willing to back up their work with a guarantee, it shows confidence in the quality of their services.
Be Clear on the Scope of Work
To get an accurate quote, it’s essential to be specific and clear about the scope of the work. Provide detailed information about your project when reaching out to contractors. The more clarity you provide, the less likely you’ll receive unexpected or hidden costs later. For example, if you’re renovating a bathroom, outline the specific tasks you want done—whether it’s replacing the tile, updating plumbing fixtures, or repainting. This ensures the contractor knows exactly what’s involved and can give you a precise estimate. It also helps avoid miscommunication and sets clear expectations for both you and the contractor.
By following these steps, you’ll be well on your way to finding the right contractor for the job at a fair price. Taking the time to ask for multiple quotes, verify credentials, inquire about guarantees, and clearly outline your project ensures that you’ll get the most accurate labor quotes possible.
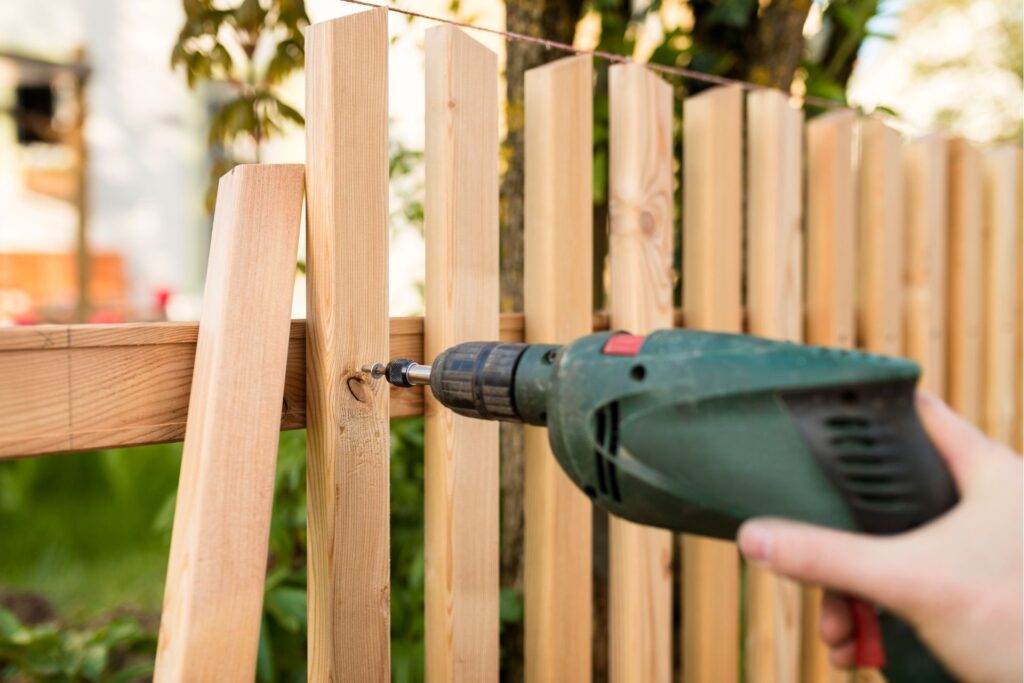
Ways To Reduce Labor Costs
Managing labor costs is a crucial part of any home improvement project, and fencing is no exception. Fortunately, there are a few smart strategies you can use to keep expenses in check without sacrificing the quality of your new fence. Here are three practical ways to lower labor costs during your fencing project.
Choose Off-Peak Season
Timing your fencing project wisely can lead to significant savings. Contractors are often busiest during the spring and summer months when demand for outdoor projects is at its highest. However, during the off-peak season—typically fall and winter—many contractors have less work lined up, which can result in lower labor rates. By scheduling your fencing installation during these slower months, you can take advantage of reduced labor costs, as contractors may be more willing to negotiate pricing to secure the job. Additionally, with less competition from other clients, you may find that your project gets completed faster.
Simplify the Design
The complexity of your fence design can directly impact labor costs. Intricate designs, such as those with custom shapes, decorative elements, or multi-level sections, take longer to install and require more specialized skills, leading to higher labor expenses. If you’re looking to save money, opting for a simpler design can significantly reduce the amount of time and effort required for installation. Straightforward styles, such as a standard picket or privacy fence, are easier to install and, therefore, less costly in terms of labor. By focusing on function over elaborate aesthetics, you can still achieve a great-looking fence without breaking the bank.
Do Some Prep Work Yourself
Another effective way to cut labor costs is by taking on some of the prep work yourself. Before your contractor arrives, you can handle tasks like clearing the installation site, removing any old fencing, or trimming back overgrown vegetation. Not only does this reduce the amount of time your contractor needs to spend on-site, but it also lowers the overall labor cost. Keep in mind that while DIY prep work can save you money, it’s essential to ensure that everything is done correctly to avoid any delays or additional charges. If you’re unsure about what prep work needs to be done, don’t hesitate to ask your contractor for guidance.
By choosing the right season, simplifying your design, and pitching in with some of the groundwork, you can effectively reduce labor costs and make your fencing project more affordable.
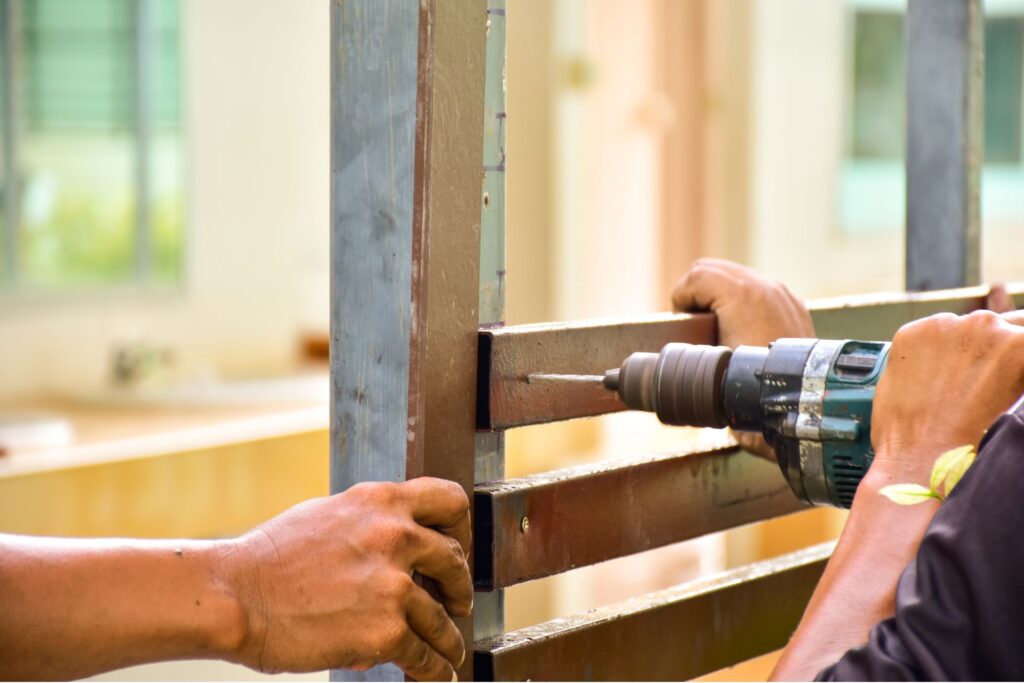
FAQs: About How Much Is Labor For Fence Installation
How much does labor for fence installation typically cost?
On average, labor for fence installation ranges from $10 to $30 per linear foot. The exact cost can vary depending on factors like the type of fence, the complexity of the installation, and your geographic location.
What factors affect the cost of labor for fence installation?
Several factors can impact labor costs, including the type of fence material (wood, vinyl, chain link, etc.), the length and height of the fence, the condition of the terrain (e.g., sloped or rocky ground), and the local labor rates in your area.
Is it cheaper to install a fence yourself or hire a professional?
While DIY fence installation can save you money on labor, it can be more time-consuming and challenging. If you have the right tools and experience, it may be a good option, but hiring a professional ensures the job is done efficiently and correctly, often with a warranty on labor.
What is included in the labor cost for fence installation?
Labor costs generally include site preparation, digging and setting fence posts, installing fence panels or pickets, attaching gates, and site clean-up. The complexity of the fence design can also affect labor costs.
How long does it take to install a fence?
The timeline for fence installation varies depending on the size of the project and the type of fence. On average, a standard fence installation takes 1-3 days, but more complex designs or larger fences may require additional time.
Do I need to prepare the site before installation to reduce labor costs?
Yes, you can reduce labor costs by clearing the area of debris, vegetation, or old fencing before the professionals arrive. However, more significant tasks like grading or leveling the ground may still require professional help.
Are there any hidden costs in labor for fence installation?
While most labor costs are upfront, additional expenses can arise from unexpected site conditions, such as hard-to-dig soil or the need for custom work like installing gates or decorative elements.
How can I get an accurate labor quote for fence installation?
To get an accurate quote, it’s essential to provide detailed information about your project, including the type of fence, the size of the area, and any special requirements like gate installation. Always get multiple quotes from local contractors and compare them before making a decision.
Does the type of fence I choose affect labor costs?
Yes, the type of fence significantly impacts labor costs. For example, wood and chain link fences are generally easier and cheaper to install, while vinyl, wrought iron, and custom designs often require more labor, raising the cost.
When is the best time to install a fence to save on labor costs?
Installing a fence during the off-peak season, typically in late fall or winter, can sometimes lead to lower labor costs, as contractors may have less demand during these periods. Additionally, simpler fence designs can help reduce overall labor expenses.
Conclusion
Labor costs for fence installation can vary based on several factors, including the type of fence material, the size of the area, and the complexity of the project. Professional installation often includes expenses like permits, preparation work, and labor, which can fluctuate depending on location and local rates. Now that you understand the key factors influencing fence installation costs, you’re in a better position to decide whether to tackle it as a DIY project or hire a contractor. To get the best deal, consider reaching out to local professionals for quotes. If you found this information helpful, feel free to share it with friends considering fence installation or save it for future reference.
About the Author:
Mike Veail is a recognized digital marketing expert with over 6 years of experience in helping tradespeople and small businesses thrive online. A former quantity surveyor, Mike combines deep industry knowledge with hands-on expertise in SEO and Google Ads. His marketing strategies are tailored to the specific needs of the trades sector, helping businesses increase visibility and generate more leads through proven, ethical methods.
Mike has successfully partnered with numerous companies, establishing a track record of delivering measurable results. His work has been featured across various platforms that showcase his expertise in lead generation and online marketing for the trades sector.
Learn more about Mike's experience and services at https://theleadguy.online or follow him on social media: